From Choir and Organ magazine — Recent technology has revolutionized our planet, and not least the world of music. Steven A. Markowitz relates the story of how his father, the founder of Allen Organ Company, pioneered digital organs 50 years ago.
Throughout industries there are examples of individuals who have changed the larger world. Some are well-known, while others focused on their trade and avoided publicity. In the electronic keyboard industry, Jerome Markowitz not only invented the first fully electronic organ, but decades later would be responsible for the introduction of the world’s first musical instrument utilizing digital sampling. This is a history of how vision, ingenuity and dedication, along with a willingness to take on risk, would change the way electronic musical sounds are produced with implications far beyond the organ market.
Digital sound is now ubiquitous, a part of all sound producing products. However, not long before the advent of CDs and MP3, all sound was created through analog technology. Remarkably, the roots of digital sound production emanated within the niche church organ field from a small company located in Macungie, Pennsylvania, USA.
In 2021 it will be 50 years since the world’s first digital musical instrument was offered for sale. The development and commercialization of this revolutionary technology is a remarkable story of one man’s dedication to creating electronic instruments of the highest fidelity.
In a sense, the impetus behind the technology that would lead to the digital organ and digital sound production was set in motion by US President John F. Kennedy who in 1961 declared: “First, I believe that this nation should commit itself to achieving the goal, before this decade is out, of landing a man on the moon and returning him safely to the Earth.” The technology required to meet this ambitious goal had not yet been developed. But, scientists and large companies determined to meet it.
Technological hurdles to be overcome before NASA could fulfill Kennedy’s vision included the miniaturization of computers so that complex calculations, such as telemetry, could
be made by astronauts in real-time on the Apollo capsule. In 1961 a computer capable of such calculations
weighed thousands of pounds. It had to
be miniaturized to the size of a small waste bin requiring significant
advancements in Large-Scale Integrated Circuits (LSI) technology. The aerospace company tasked with resolving
this challenge was North American Aviation, later to become North American
Rockwell.

Because of Rockwell’s expertise in rocket technology, it was also a prime contractor for the Apollo program with thousands of employees dedicated to it. In 1966, three years before the first American would land on the moon, Rockwell understood that US spending on the Apollo program would wane in a few years. To offset this inevitable revenue loss, Rockwell’s management created a strategic plan for the company to utilize the advanced technology it developed for the space program in commercial products. These products would then require Rockwell’s LSI circuits and create a longer-term revenue stream. As the home organ business was booming in the mid-1960s, an idea spawned by one Rockwell scientist was to use digital technology to produce organ sounds.
Since Rockwell had no organ or music expertise, it needed a joint venture with an organ manufacturer to co-develop the digital organ. The plan was that Rockwell would supply the technology and LSI circuits, with the organ company supplying the musical and business expertise. Also, Rockwell, using a practice common with government contracts, expected the organ company to pay for the development cost for a commercially viable digital organ.
After a small proof of concept project, Rockwell contacted all the major American home organ manufacturers including Hammond, Conn, and Wurlitzer proposing a joint venture. While these companies were interested in the revolutionary technology, they were unwilling to invest in it until Rockwell would create an actual working organ. Rockwell was unwilling to make this investment and the digital organ project was on the verge of being cancelled. As a last-ditch effort to save the project, Rockwell contacted a small organ manufacturer, Allen Organ Company.
Allen Organ Company, founded by Jerome Markowitz in 1937, had always been on the cutting edge of analog sound technology. While attending Muhlenberg College in Allentown, Pennsylvania, Markowitz was enamored by the sound of the pipe organ
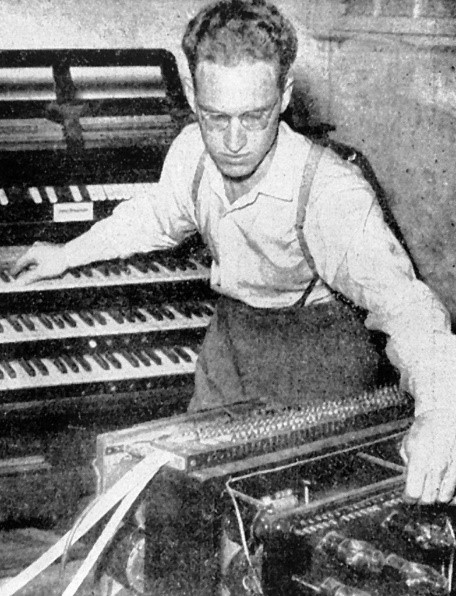
in the College’s chapel. In his book, Triumphs & Trials of an Organ Builder, he stated: “The intricate patterns of sound created by the big, sustained chords especially fascinated me”. In the early 1930s, there was only one electric organ, the Hammond Organ. It was compact and inexpensive compared to pipe organs, which intrigued Jerome. However, the Hammond’s electro-mechanical tone generation system could only create sounds appropriate for popular music. It could not produce sounds required for classical or liturgical music. Markowitz then decided to dedicate his life to producing pipe organ sounds through electronic tone production means.
Markowitz was a self-taught electronic engineer with expertise in radio and vacuum tube technologies. During the second World War he was sent to Hawaii to work on advanced radar systems. Prior to the War he resolved the technical problem that hindered the production of musical sounds by electronic means, the need for stable tuning oscillators. In 1938 he was granted United States patent US2140267A for the Stable Oscillator. This technology would lead to the first fully electronic organ and the birth of Allen Organ Company.
Through the 1950s and 1960s, Markowitz introduced numerous innovations and was granted patents that included low frequency oscillators (US2190078A), space discharge harmonic generator (US2329069A0), rotatable loud-speakers (Gyrophonic) with stationary baffle (US2491674A), circuit for tuning oscillators (US2939359A), Chiff characteristics (US2989886A), solidifying Allen’s leadership in analog organ technology. The Company enjoyed significant success with thousands of analog organ installations made worldwide.
By 1967, when Rockwell approached Allen about the joint venture, Markowitz was the world’s premier analog tone generation engineer. He immediately understood the revolutionary potential of digital tone generation, later called “sampling”. He focused on the technology’s ability to accurately reproduce complex pipe organ waveshapes. For years he had struggled with analog technology’s limitations to create realistic organ principal stops, the foundation sounds for classical pipe organs, but by the mid-1960s he had concluded the technology had limitations and reached its zenith. Therefore, he was willing to radically change the Company’s technology and direction to accomplish his tonal goals.
In 1967, when Allen Organ Company entered the joint venture with Rockwell, Markowitz bet the Company’s future on the technology, a risky bet. To produce a commercially viable digital organ would ultimately require 13 unique custom LSI circuits, a project so large that nothing of similar scope had yet been attempted by any commercial company in any field. In fact, the Allen digital organ would be only the second commercial product ever to utilize custom LSI circuits, with the first being the Sharp calculator. The technology behind these circuits was then known as MOS (Metal–oxide–semiconductor).
As a young teenager in 1967, while aware of the digital organ project, I did not understand its significance. But in 1969, in the same week that Neil Armstrong walked on the moon, I visited Rockwell facilities in Anaheim and El Segundo, California with my father. There I was instructed on LSI technology by Rockwell engineers, and saw a demonstration of laser technology. I recall being schooled on Epitaxy growth, a basic process for the creation of MOS circuits. Heady stuff for a 15-year old!
The joint venture called for Allen to invest US $2 million in the digital organ’s development, a massive amount for a company with sales of less than US $8 million. After the agreement was signed, the engineering work on the digital organ would take over three years and required resolving significant technical issues. More than a year into the digital organ’s development, significant tuning deficiencies were discovered by Allen, an issue Rockwell had not recognized during the development. Ironically, this was an issue Jerome’s invention had resolved 30-years earlier for analog tone-generation technology. Once again, the project was again almost cancelled. Ultimately, the problem was resolved, but required additional hardware and increased the engineering development time.
While advanced technology was a crucial component for developing a digital organ, technological-artistic input was also required in the recording and processing of pipe sounds. Cohesive ensembles had made the pipe organ The King of Instruments. This was also a requirement for a successful digital organ. These musical-engineering tasks were the responsibility of Allen Organ Company, more specifically Markowitz.
Digital sampling begins with recording pipes with this information ultimately stored in the organ for playback. Markowitz spent months experimenting with different means to record organ pipes for sampling. The simplest method is to place the microphone out in the building in which the organ is installed, distant from the pipes, and to just to record from one location. This technique was found to be unacceptable since the recordings would also include distortions caused by the building, as well as extraneous room noises captured during the recording process that were accentuated by the higher microphone input gains needed to capture the distant pipe sounds. Any attempt to eliminate the unwanted noises through filtering mutated the original pipe sound. This recording technique is known as “Wet Sampling”.
Some companies today offer “Virtual Organs” using PC tone generation and Wet Samples, a recording method that offers advantages to these suppliers. Wet Sampling is a simpler and less expensive process for recording pipes. In addition, Wet Samples require less processing power and therefore allow for the use of less powerful tone generators. With Wet Samples there is little attempt (or ability) to optimize individual sounds or how they work together within ensembles. What is recorded is what you get, including room distortions and extraneous noises. And last, Wet Samples include some of the original room’s acoustics that then comes in conflict with the acoustics of the building in which the digital organ is ultimately installed.
To create pure pipe sounds, Markowitz learned that the microphone needed to be placed very close to each pipe, which also offered the optimal signal-to-noise ratio for the recordings.
These pure sounds could then be processed, as all sample sounds must be prior to being stored in a digital organ, without the distortions and extraneous room noises. This “Dry Sampling” technique, which Allen continues to use to this day, allows the digital sounds to be individually voiced, as a pipe technician needs to voice individual pipes. This process leads to the grand ensembles found in fine pipe organs. It is tedious work whether the sounds are produced from winded pipes or digital sampling. After the pipe recordings were made, significant musical engineering work was required to prepare them for
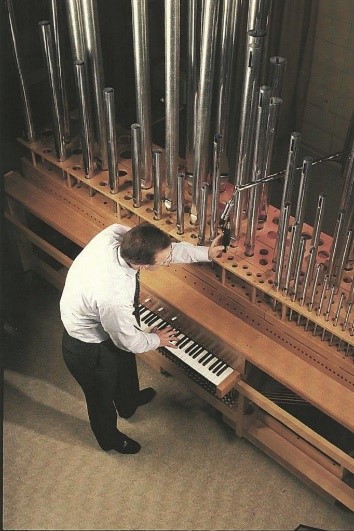
storage in the organ. In the late 1960s this necessitated the use of a large IBM mainframe computer which were rare. GAC (General Acceptance Corporation), a financial company in Allentown, PA, allowed my father access to their computer. These sampled sounds were then worked on for many hours using the secret engineering model located in our house. This work had to be nearly perfect since, at the time, all sampled sounds were encoded at great expense in hard memories with Allen having to commit to the purchase of thousands of these unchangeable LSI memory circuits.
After Allen introduced the world’s first digital organ in 1971 it was quickly recognized for its tonal quality and revolutionary technology. The Allen Digital Computer Organ would precede most competing digital church organs by more than 15 years. The invention earned Jerome Markowitz the coveted IR-100 Award as one of 100 most significant innovations of that year. Also, demonstrating the significance of Allen’s Digital Computer Organ is that the first instrument is housed at the Smithsonian Institution. This technology brought sampled pipe organ sounds to churches worldwide, many of whom could not afford a pipe organ.
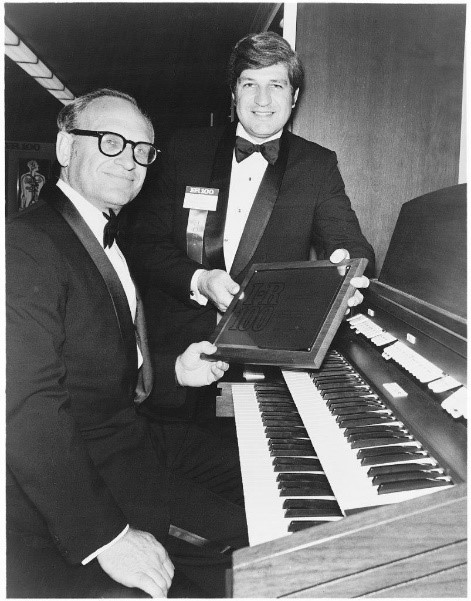
The Allen Organ Company/North American Rockwell joint venture was not without strains. After the introduction of the Allen Digital Computer Organ at the 1971 (National Association of Music Merchants, NAMM, in Chicago, Illinois, a conflict developed between the companies. To my father’s surprise, Rockwell started to market the technology to other companies, even though the Joint Venture Agreement required Allen’s approval first. At the NAMM show Rockwell brought in approximately twenty Yamaha engineering personnel, as well as its President, Genichi Kawakami, for a private showing of the Allen Digital Organ.
Though Allen’s focus at the time was on stabilizing the digital technology and production requirements for the organs, Rockwell’s was to maximize the sale of LSI circuits, which had them turn to the larger home organ market in which Yamaha was a growing force. The disagreement grew and lead to lengthy litigation, which ended in Allen’s favor.
By the mid-1970s Allen had resolved the technical and production challenges with the digital organ. Allen owned the musical instrument patents for digital sound technology and the digital organ dominated the church organ market. The Company then made the strategic decision not to monopolize the technology, but instead offer patent licenses to other organ and synthesizer manufacturers, ultimately entering into agreements with most keyboard musical instrument manufacturers, including Yamaha. Those that did not take a license remained committed to analog technology until the patents expired in the late 1980s.
The
basic Rockwell technology was utilized by Allen until 1982 with generational
leaps made since. Allen’s latest
GeniSys™ Technology features not only advanced digital tone
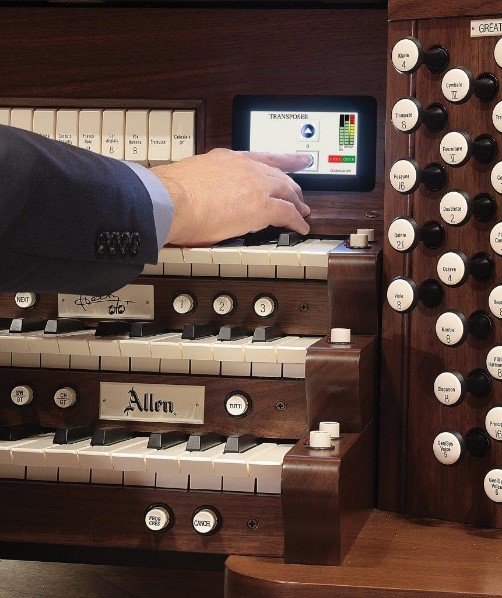
generation, but a user-friendly touchscreen interface, convolution acoustics, smart phone accessibility/Wi-Fi connectivity, and 250 dynamic (changeable) high-definition voices. In addition, through proprietary voicing software and its SoundMatrix™ Library, Allen voicers can meet the tastes and expectations of even the most demanding organist. Finally, Allen’s Stoplist Library™ allows organists to explore different schools of organ building including American Classic, English Cathedral, Cavaillé-Coll, Arp Schnitger, Schlicker, Aeolian-Skinner, as well as multiple theatre organ suites, at the touch of a screen.
Thanks to Markowitz’s vision and dedication, Allen Organ Company was the innovator for both analog and digitally sampled organs. My Father passed away in 1991, a year after I became President of Allen. The mission of the Company remains unchanged to this day; to bring the finest pipe organ sounds produced electronically to churches and consumers worldwide.
Throughout Allen Organ Company’s eight-decade history, it has installed some 80,000 instruments in over 70 countries and employed thousands of workers. Steven A. Markowitz is the president of Allen Organ Company and son of its founder, Jerome Markowitz.
i